第1回『なぜ設計開発領域の改革が上手くいかないのか?』
SCM(サプライチェーンマネジメント)改革という言葉が使われるようになって数十年が経ちます。1980年代にコンサルティング会社が使い始め、1990年代後半には米国でサプライチェーンカウンシル(SCC)が運用参照モデルとしてSCORを開発し、その手法がグローバルに広がり日本でも多くの企業が導入してきました。反面、DCM(デザインチェーンマネジメント)と我々が呼んでいる設計開発を中心としたモノづくりの領域に関しては部分的な改善に留まっているのが現状ではないかと思われます。
SCMだけでは競争に勝てない
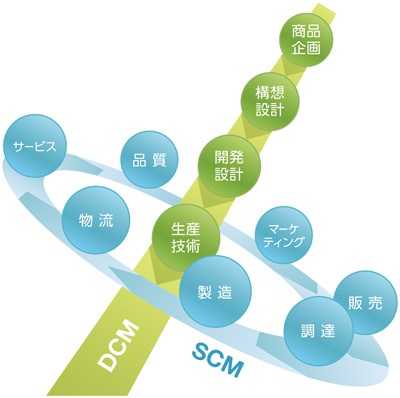
DCM(設計開発領域)の改革が進まないわけ
では、なぜDCM領域の改革は進まないのでしょうか? 図2にSCMとDCMの比較をしてみました。SCM領域は様々なものが揃っていますが、DCM領域ではまだまだ未成熟に見えます。そもそもDCMという概念も共通ではありません。実はこれには非常にシンプルな理由があるのです。
図2.SCMとDCMの比較
SCM領域では、比較的短期間に効果を出すことができ、かつROIが明確だという特徴があります。例えば在庫の削減量がプランニングできれば、効果額が簡単に計算可能です。そのため、トップダウンで投資をするにもリスクが少なく、判断しやすいといった事があげられます。
逆にDCM領域では、設計開発プロセスの短期化や技術蓄積による高付加価値製品の開発が必要なことは十分理解しているものの、効果創出には時間がかかり、かつROIが非常に見えにくいというのが現実です。開発期間が半減されれば競合に比べ早く市場に製品を出すことができるため先行者利益を得られますが、それが幾らになるのか?半分の人数で開発ができる!といった時に、では開発者を削減できるかといえば、それはすぐにはできないことですし、そのコストはSCMの在庫削減に比べれば非常に小さく見えます。結果的にトップがよほどこの領域に対する意識がなければトップダウンでの実施は困難で、どうしても部門内での業務効率化を中心とした改善活動にとどまっているのが現実です。
DCM(設計開発領域)における経営者の悩み
DCM領域での経営者の悩みを聞くと下記のようなコメントを多く聞きます。
新製品が予定通り出ないというのは販売戦略上も致命的ですし、営業部門の新製品を見込んだ提案活動ができなくなってしまいます。65歳以上の再雇用のベテランや外注会社のベテラン設計者頼みの開発になっている会社も多く見受けられます。また、ある事業の製品をずっと担当し続けて横の交流も技術もなく、新製品開発が進まないといった悩みもよく耳にします。開発に必要以上の手戻りが入ることで、開発者は時間が取れず、顧客ニーズを組み入れた製品開発など、やる余裕がないといった本末転倒な状況があります。
こうした問題をトップも認識しているにかかわらず改革が進まない、といった状況をどのように打破したらよいのでしょうか?
トップダウンとボトムアップをビジネスと技術でつなぐ
私が所属する組織名の「共動創発」。この中の「創発」とは、「トップダウン」と「ボトムアップ」双方向のルールを明確にすることで新たな価値が生まれるという考え方です。図3にある三つのレイヤーを定義し、Business/Product/Intelligenceの各レイヤー、各要素間の相関関係をトップダウンとボトムアップ双方向アプローチで解くことが重要です。
図3.創発アプローチの考え方
特にDCM領域では、ProductとIntelligenceの2レイヤーで改革活動をする事が多く見受けられます。製品構造の見直しやモジュール化、標準化といった手法、ナレッジを形式知化して活用するといった事が主たるテーマとなっています。開発・設計業務を行いながら、これらの改革活動を行うためには、現場の必要性認識だけでなく、トップからの支援(投資、人的リソース強化、ビジネス判断での業務変更等)が必要になるのですが、この2つのレイヤーだけだと、経営トップは現場で解決すべき問題として認識してしまいます。
ここで重要な事は図のようにこれらの2レイヤーとBusinessレイヤーをつなげる必要があるのです。Businessレイヤーとつなげる事で開発設計現場の改善活動ではなく、ビジネスに貢献するための活動だという事をトップに認識させ、トップの意思をいれた活動に昇華させる必要があるのです。この3つのレイヤーが有機的につながることで、経営トップからすれば経営への貢献が明確になり、トップダウンで進める動力となり、開発設計の現場からすれば自分たちが必要な打ち手を上位層の認識のもと、投資をしてもらいながら活動することができるのです。 その方法については様々ですが、次回のコラムで詳しくご紹介します。