第4回 設備異常発生率が約半減に。稼働後のリアルな数値変化
稼働後のリアルな数値変化と、その後
本稼働直後は「途中で操作が分からなくなった」というような不慣れさに起因する点検ミスが発生したが、3ヶ月後からはほぼすべての点検をiPadアプリで行うことができ、完全に定着したと判断。設備異常発生率は、なんと稼働後翌月には約半減するという、想像以上の効果が出始めました。
なぜ、こんなに瞬間的に効果が出始めたかと言えば、やはりデータとして見えるようになり、意識が大きく変わったことが最大の要因だと我々の中では分析していました。これまでの「点」ではなく、「線」としてデータを見ることで打ち手を打っていける。製造現場には、この打ち手を出す力は十分に秘められていますが、そのための情報の活かし方が上手くないというのが、今の製造現場の実態なのだと思います。
実際の、作業実施率/OEE(総合設備効率)/設備異常率の推移がこちらになります。
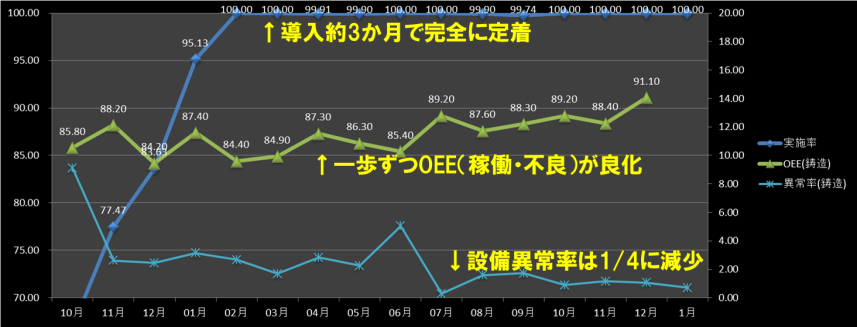
もし、月並みな宣伝文句で言うならば、「導入翌月には設備異常が半減!」と瞬間最大風速を前面に打ち出してアピールするところですが、製造業はその時だけ良くても意味なし、継続的に効果を発揮させられているか?ここがキモだと考えています。つまり、このグラフ(導入15か月後)以降、どのように推移していったのかを正直に伺ってみました。
実際のユーザーの目線から・・・
本稼働から6年以上経過した今も、iPad+点検アプリは設備点検で毎日使っています。点検内容のメンテは、システムで言えばマスターメンテのようなものですので、最低年一回行って見直しを続けています。同時に朝礼の報告も形式をすいぶんと変えてはいますが、未だに少しずつ進化させています。
設備異常率については、マシンはますます劣化しているのですが、攻めの予防保全をというテーマで劣化に負けない工場を心がけており、月ごとに上下はあるものの、このグラフの最後の数値よりも少し良いという状態をキープしています。ここまで異常が減ると、設備点検から導き出せる対処だけでは大幅に減らすのは難しいな・・・というのが本音ですね。
むしろ、点検データを元にして、保全作業の頻度が高い部分の部品を見直したり、オーバーホールでしっかり対応させたり、日常ではできない改良や改修の計画に利用をしています。
一瞬良くなったけど、またダメになったというのでは意味がなく、やはりこのように継続的に効果を出していくことが「成果」というのであれば、成果を出していることは間違いないと思いますね。(佐野氏)
IoTの取り組みについて
では、同社はIoT化をどのように進めている、または進めていくのだろうか?と最後に質問しました。
実際のユーザーの目線から・・・
当社は結局「人力IoT」を2011年から行っていたというのが分かりやすい表現だと思います。この人力の部分を設備から自動で取得できるのが、本当のIoTでしょうね。
どうしても人力だと、24時間・一切途切れることなく情報収集するのは無理。IoTならば暑い日も寒い日も24時間情報収集してくれるので、そこで情報の密度は劇的に変わるという受け止め方をしています。しかしIoT化する上で非常に気を付けている点もあります。それは「情報の波に呑まれない」ということ。
つまり情報量・密度ともに大きくなるので、きちんと目的意識を持ってデータを活用していかないと、結局収集しただけ、使われない宝の山になり兼ねないという危機感を持っています。幸い、当社はこのように点検などのデータを活用するPDCAが回っているとは思いますが、今後の本格的なIoT時代に対しては、脆弱と感じています。
ですので、今進めているのは、BIツールを使った分析力強化と、即効性あるIoTの積極活用です。情報レベルが変われば、分析レベルも変えるのが当然ですので、BIツールでもっと直感的に論理的にデータを拾って判断のスピードを上げるというのがひとつ。もうひとつは、点検IT化と同じく、成果の果実をいち早く手に入れ、そこを踏み台にして加速していくということですね。良いことや改善は一秒でも早く、実施して手に入れるという考えです。(佐野氏)
IoT時代の遥か前から、人力IoTという方法で工場のデータ収集・活用を行ってきた同社の進め方は、本物のIoT時代の今も十分に通用する「原理原則」ではないかと思いますが、皆さんいかがでしょうか。現在、働き方改革プロジェクトは解散したものの、旭テックアルミニウム株式会社は上記のように、BIツールの活用と即効性あるIoTに引き続きトライしていました。
まとめ
- 何を目標にするか?抽象的なIoTの夢ではなく、実際の業務ベースのIoT推進を
- データ取得は目的ではなく、活用のための徹底フォローでデータを活かす
- 作業者に負担を掛けず、改善効果を手に入れる
- 小さなコスト(またはトライアル)でスタートし、徐々に拡大させる
- 情報の波に呑まれないようポイントを絞って、BIツールなどで使えるデータへ
非常に印象的だったのは、既に労働力確保が少しずつ難しくなっており、今後その流れは加速していくのは間違いないのだから、「人は人にしかできない仕事をするべき」という言葉でした。IoTで出来る部分はIoT化し、人はもっと働き方を変えないと、いずれ工場は人手不足で操業できなくなると危機感を持っており、その対策を今からIoTで考えるという切り口は日本の製造業におけるIoT利活用のひとつの指針になるかもしれません。
今回はIoT前夜という時代から、データ収集・活用を進めてきた実例を記載しましたが、次回は東南アジアでIoTを導入し、実態把握に成功した事例をいよいよご紹介したいと思います。
第1回目から読む場合はこちら