第2回:ハイブリッド生産方式への転換前にすべきこと
標準化は着実なステップで行う
ハイブリッド生産方式への転換は、その過程において否応なく設計プロセスを改革の方向へ後押しします。調達LTの短縮は、モノの共通化・標準化を前提としていました。しかしその共通化・標準化は、どこが行うのでしょう?
そうです。言わずもがな、設計開発部門が実施することになります。しかも方式転換に先行(並行)して。ハイブリッド生産方式を生かすも殺すも、モノの共通化・標準化次第と言えます。
しかし、そもそも「標準化をどのように進めるべきか」について、個別受注生産企業の多くが悩まれているのではないでしょうか。
個別受注生産は、顧客に寄り添って要望に細やかに応えることで要求品質に対する満足度を高めています。そのため、下手に標準化や汎用化を進めてしまえば、顧客の要望に沿うことができなかったり、設計の自由度、柔軟性を損なうことで品質低下を招いたり、といったことが起こり得ます。また、標準化をすることで、これまでとは業務の進め方を大きく変えなければならないケースも出てくるので、これは特に経験年数が長いベテランにとって少なからずストレスになることでもあります。
標準化には、多くの部門・利害関係者を跨ぐ難しさがあり、ともすると感情的な問題も引き起こしかねないことから、関係メンバーのモチベーション維持やマインド醸成をいかにうまく行うか、検討着手前から十分に考慮しておくことが重要です。メンバー同士で丁寧にコミュニケーションを取りながら目的や期待する効果を共有する機会を作り、ひとつひとつ階段を上るように取り組みを進めていくしか道はありません。
千里の道も一歩から。まずは共通化から
標準化の進め方としては、まず以下のように部門ごとにブレイクダウンして、手順整理やドキュメント化などを地道に進めていきます。
- 設計部門:①2Dから3D設計へシフト、②部品・ユニット共通化、③仕様-機能の関連整理=「モジュラーデザイン」による標準化
- 生産技術部門:適切な製造手順設計、ドキュメント化
- 品質保証部門:適切な検査手順設計、計測基準の設定、ドキュメント化
- 営業部門:仕様選択型販売への対応、提案型営業スタイルへのマインドチェンジ
過去の派生機種、部品属性の1つひとつまで、全てを俯瞰的に見渡して確認し、共通化要件を探っていくことはとても骨が折れる作業です。図面や紙文書などアナログ情報が混在すれば、その手間や時間は指数的に増大することになります。
標準化の前にまず共通化と腹を据え、アナログ情報のデータ化、データへの意味関連付け(タグ付け)を地道にこなすことがゴールへの最短ルートになります。
標準化を加速する3D設計
設計を2Dから3Dへシフトするのは、設計プロセス標準化の加速に加え、部品標準化、ユニットモジュール化実現の強力かつ有効な手段になります。3D設計は2D設計と比べその自由度が著しく制限されます。CADオペレーションの難易度も上がりますが、扱う次元が増えることで制約がシビアになり、曖昧性に対する許容が厳しいものになるのです。一見、デメリットのようにも感じるこれら制約ですが、実はこれこそがプロセスおよびモデル(部品やユニット)標準化を否応なしに加速させる鍵になっています。
下図は、3Dモデルのジオメトリ情報を使い、タグ付けの手間を掛けずに共通部品やユニットを抽出・分類する仕組みの実現例を示しています。共通化は3D+PLMで楽をして実現できる時代になっています。
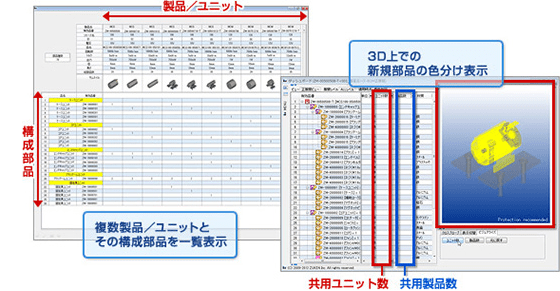
これまでは、標準化が難しいとされる業界特性と、自由度を犠牲にするこの制約が、残念な方向でマッチしてしまい、個別受注業界での3D化定着を阻害する原因となっていました。しかし、3Dは2Dとは比較にならないほど多くの情報を持つことができ、伝達能力も段違いに優れています。コンカレントエンジニアリングによる設計・生技・購買・製造の並進課題検討の実現、設計リードタイム短期化の実現に向けて、3D設計に着手してみてはいかがでしょうか。
終わりに
ハイブリッド生産方式への転換に対する先行要件として、モデル標準化の流れをご紹介いたしました。本シリーズでは、プロセス標準化技法(モジュラー化メソッド)については詳しく触れておりません。そちらにご関心ある皆様は弊社別コラム『設計部門効率化を目指す設計モジュール化技法の基礎と実践』が参考になると思います。ぜひご一読下さい。
次回は、品番とBOMについてお話します。